During my final year of undergraduate study, I delved into an unconventional engineering entrepreneurship course. This led to the creation of a 3D printer calibration tool—a project born from a desire to simplify the often intricate calibration process while maintaining affordability and compatibility.
As an avid user of a home-built 3D printer, I recognize the immense potential of 3D printing technology, yet the inherent complexities and technical depth have confined it to enthusiasts. My goal with this project was to democratize 3D printing by addressing one of its major pain points: calibration.
The Challenge
Calibrating the gap between the printer nozzle and the print bed is a perennial challenge in the setup of any print job. The traditional method involves sliding a piece of paper between the nozzle and the print bed to gauge the distance. This method is time-consuming as it often requires multiple iterations for better accuracy. Existing automated solutions are often limited by specific hardware requirements, hindering their widespread adoption.
A Simplified Solution
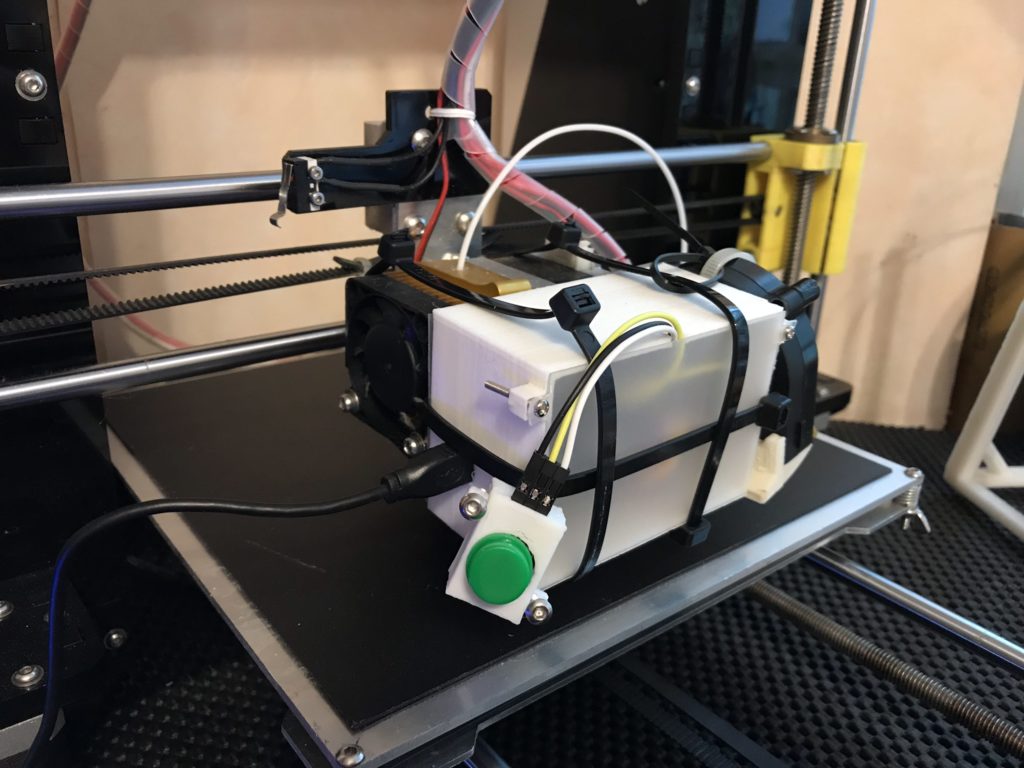
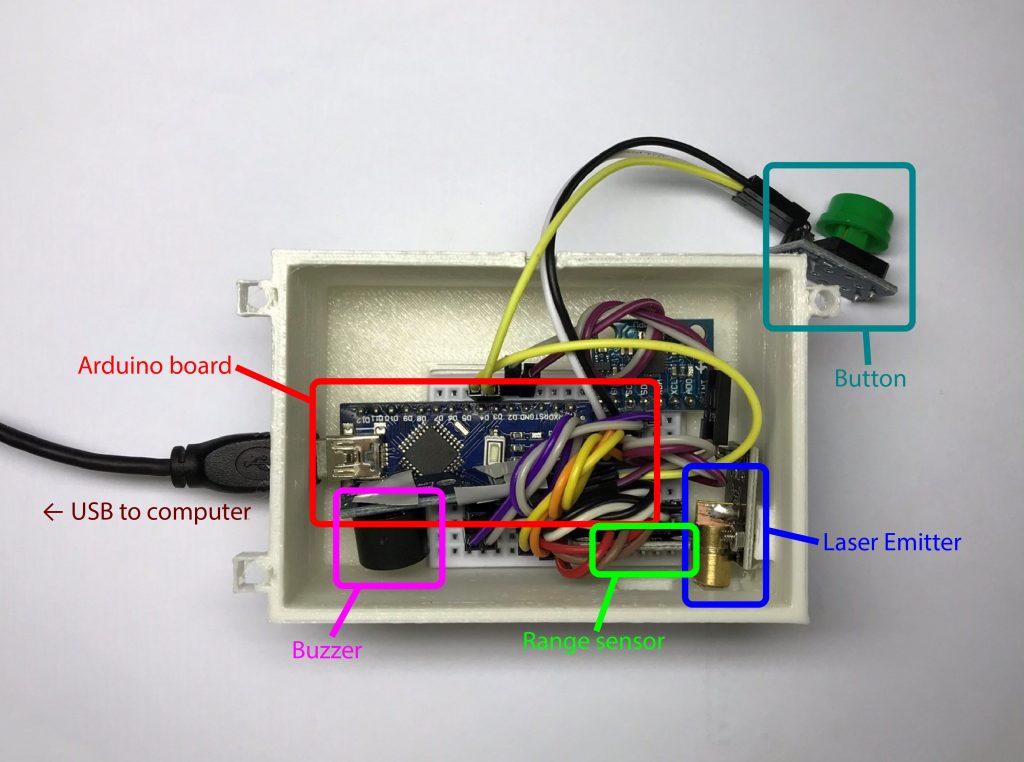
Enter my solution—a versatile add-on device designed to streamline the calibration process for a wide range of 3D printers. It provides quantified adjustment suggestions through mathematical calculations based on accurate infrared range measurement results. I developed a prototype based on Arduino to demonstrate its functionality and conducted extensive testing. The device offers a tangible improvement over manual calibration methods, promising greater accuracy and efficiency.
Looking Ahead
Venturing into embedded hardware development with Arduino was a departure from my usual focus on network security and distributed systems. Despite the initial learning curve, I discovered the remarkable versatility of Arduino boards and their potential to augment my expertise in 3D printing. I am excited to continue exploring and leveraging my skills to develop solutions to technology pain points.